Choosing the right end mill could be a really hard thing.
CNC Milling is the procedure of using cutters to remove material by feeding it onto a workpiece. Although it is one of the most ordinary methods for machining parts to meet the precise tolerance, the selection of cutters can be complex.
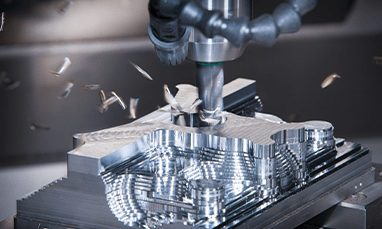
Tianzhao Cutter is a mill cutter specialist, manufacturing end mills and other cutting tools and accessories from China.
An end mill is a common cutting tool fitted on a CNC machine.
It is often used in a lathe or machining center for shaping metal or other hard non-metallic materials using rotary cutting action.
There are many types of milling cutters and the type of cutter should correspond to the material being milled, speeds, and feeds.
Check out our tips on how to choose the right end mill.
What Should Consider When Choosing End Mills
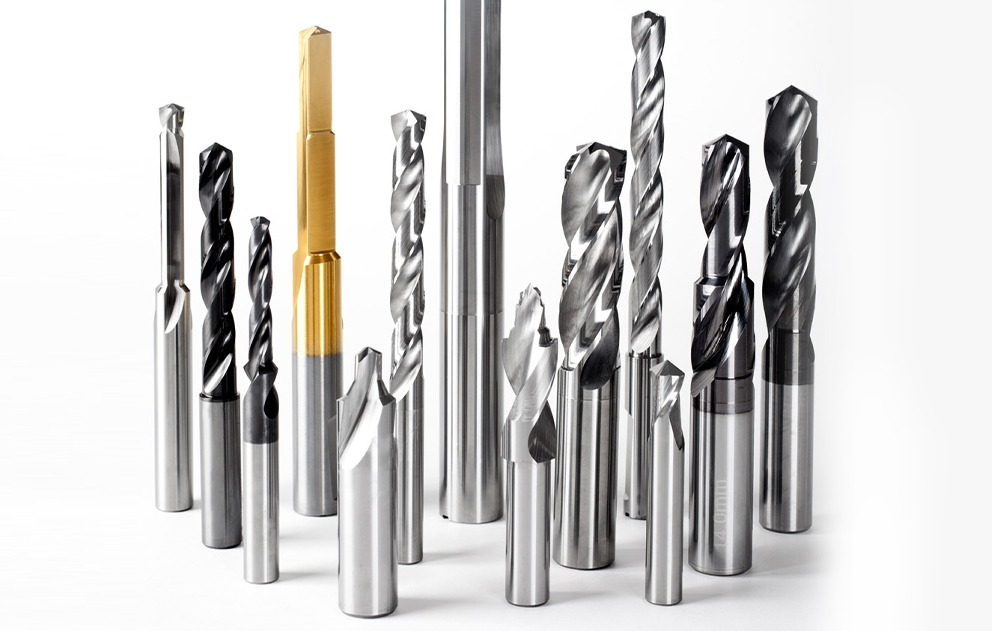
An end mill is a cutting tool used for industrial milling. It differs from a drill in application, geometry, and manufacturing. Drills can only cut in the axial direction, while most milling bits can cut in the radial direction.
Not all cutters can cut axially; only those that are designed to cut axially are called end mills.
When preparing for the making process, you may encounter questions about which type should be adopted for your CNC machine.
There are several key factors you should take into consideration:
- The parameter feature of end mills
- The shape and type of end mills
- The material of end mills
Now we will introduce the fundamentals of end mill science.
Parameter & Features
Here is the basic illustration of the feature of an end mill. End mills are in different shapes and sizes including diameter(D), cutting length(Lc), shank diameter(d), overall length(L), flutes, and helix angle.
The parameters of end mills are directly related to the usage and performance of the CNC machine.
Pay attention not to choose the wrong cutting tool. Otherwise, it might cause great damage and inconvenience to your milling process.
1. Diameter (D) & Shank Diameter (d)
End mills with larger diameters are able to remove material more efficiently than smaller ones. Therefore, the biggest one suitable for your work is recommended.
While the diameter is restricted by the scale of internal curves, which means the radius of the cutter cannot be larger than the smallest arc.
What are the benefits of enhancing the diameter of cutting tools?
Firstly, tools with larger diameters allow you to cut much deeper.
Also, it increases the stability and rigidity of your machining procedure.
Then, the larger the diameter is, the more material can be removed compared with smaller ones.
You can do your job much more effectively and efficiently by milling cutters in larger diameters.
2. Overall Length (L) & Cutting Length (Lc)
The deeper you attempt to mill, the longer the cutting tools should be.
Thus, the milling process can be successful and smooth. To put this simply, the length of it depends on the depth you want to cut into the material.
How long is suitable for my machining process?
You should keep in mind that the overall length must not be shorter than the flute. Otherwise, it will pose a huge threat to your milling process and damage the machine.
So Longer is better?
It does not mean that you should purchase end mills as long as possible to fit in any situation. If it is too long, the stability of tools will be weakened, or even worse.
3. Flutes
Most of the flutes of end mills are helical grooves winding up one side of it. A milling cutter has more than one flute end, and usually 2-flute, 3-flute, and 4-flute.
How does Flute Count impact the milling?
Feed Rate
The feed speed is related to the number of flutes. For example, a 4-flute one can remove materials twice faster than the one with 2 flutes.
Material chipping cleaning
Although a bigger number of flutes helps enhance productivity, it reduces the space for chipping materials.
If you are removing materials like plastic and aluminum with a four-fluted one, the space will be too short for clearance, which may lead to a jam of chips.
Generally, more flutes increase the feed rate, while a smaller number of flutes leads to better chip clearance.
4. Helix Angle
The flutes of tools are usually helical. If the chipping flute is linear, the whole tool will impose an impact on the material immediately, causing a vibration that leads to a decrease in preciseness and surface quality.
Setting the chip flutes at an angle allows the cutting edge to penetrate into the material gradually and reduces vibration. Usually, finishing tools have a higher helix angle to obtain better machining.
Types & Shapes
The types of end mills are generally classified according to their shape. The following is a short review of common ones.
Square End Mill
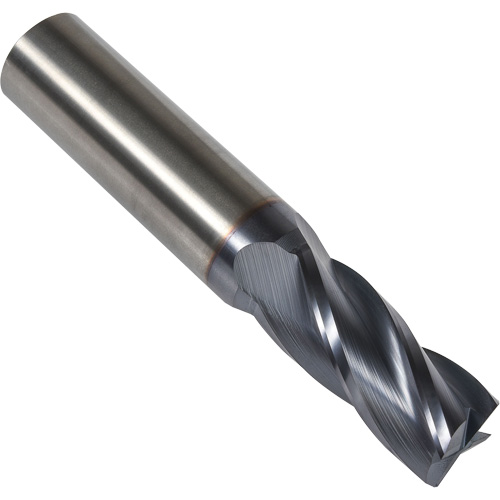
A square end mill has a square shape. The cutter is configured at the outermost and is used for cutting horizontal or vertical surfaces. It is the most common one in milling applications. It is also called flat-end mills.
Ball Nose End Mill
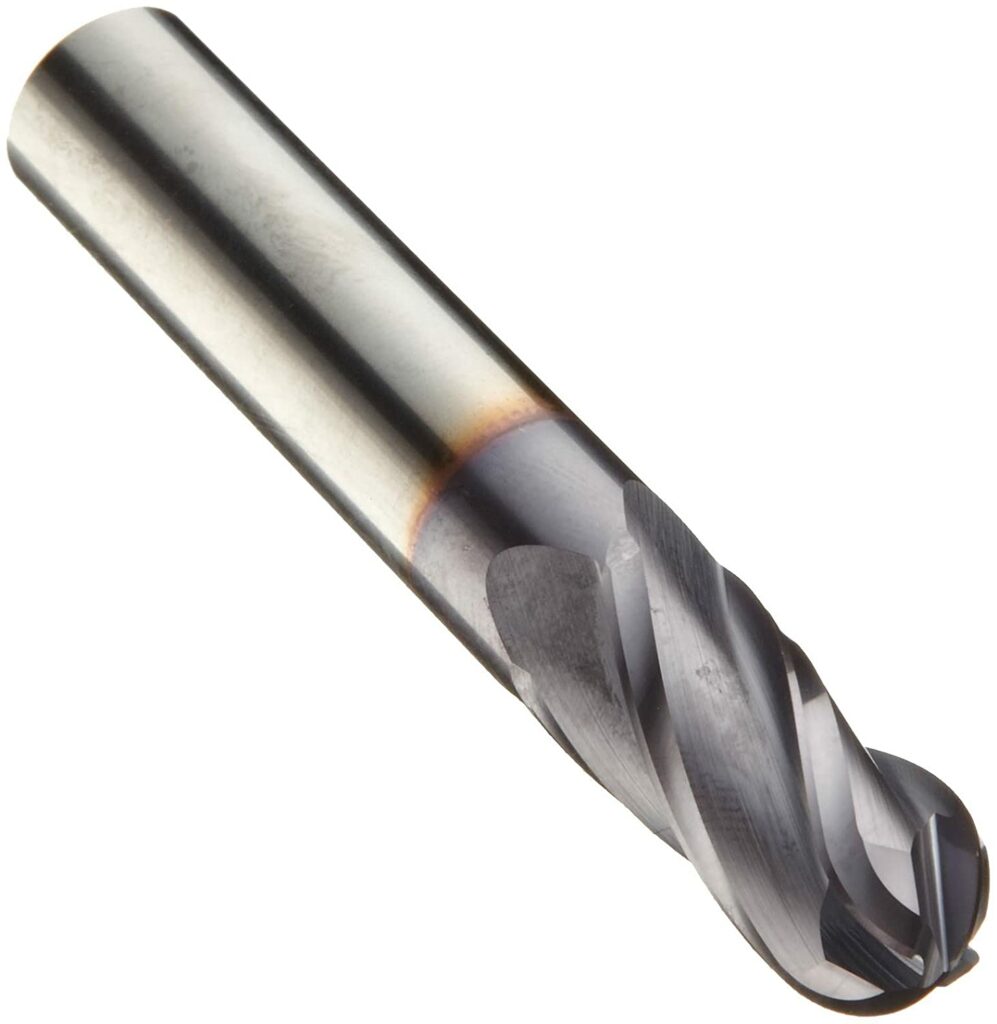
Ball end mills have semi-spherical tips and are mainly used for cutting curved surfaces. They are ideal for machining 3-dimensional contoured shapes in machining centers, for example in molds and dies.
Also, due to the extensive use of CAM in modern days, they are more widely used for finishing operations. It is often used to mill 3D shapes or circular grooves.
Roughing End Mills
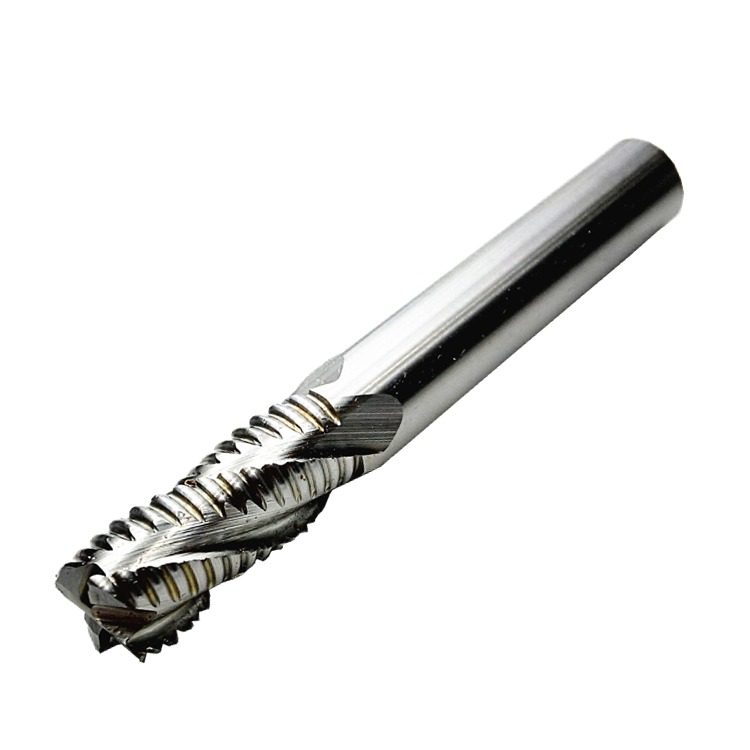
Different types of milling cutters can be used to cut large amounts of material, leaving a poor surface finish (roughing), or to remove less material, but leaving a good surface finish (finishing). Roughing tools may have serrations for breaking up pieces of material into smaller pieces.
The tip shape of a roughing end mill is similar to that of a square end mill, but the side cutting edges have wave-like irregularities that allow a larger cutting depth of cut than that of a square end mill. It removes a mass of material during heavy operations. However, its shape results in a rougher cutting surface.
Corner Radius End Mill
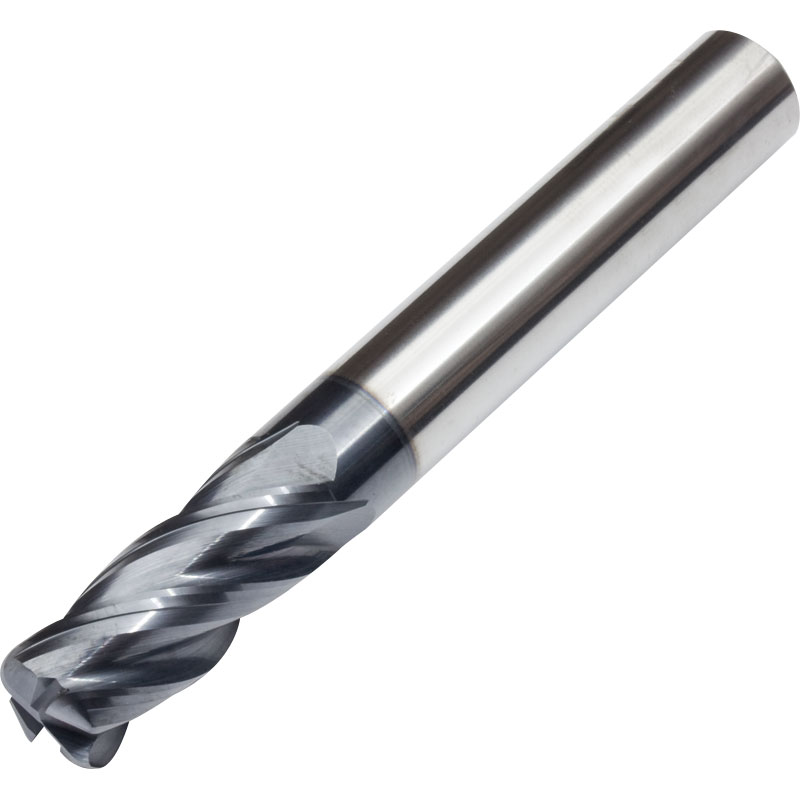
Radius end mills can be used for roughing, semi-finishing, and final finishing because the lower corners of square end mills are R-shaped. It is also known as bull-nose end mills. Its round corner helps scatter the milling force to protect the end mill and extend its tool life.
End Mill Materials
There are two commonly used materials for manufacturing end mills. One is high-speed steel (HSS), and the other one is carbide. Material is another significant matter to be considered in choosing the right end.
High-Speed Steel (HSS)
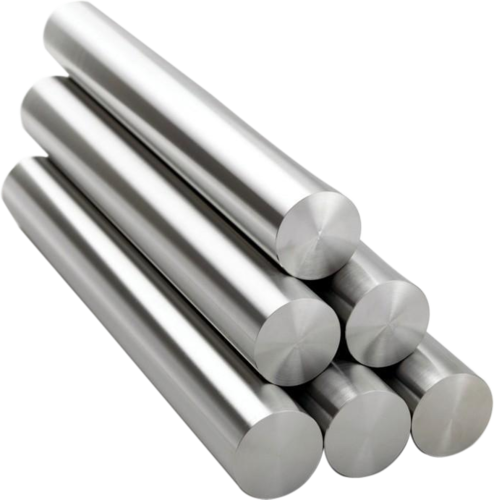
HSS is one kind of tool-making steel, usually used as a milling cutter material. It is named high-speed steel because of its ability to withstand the high temperatures generated when cutting metal at high speeds and maintain its hardness.
It is the cheapest of the two, providing nice wearing resistance, and can be applied to older, slower, or less rigid machines, and for one-off or very short runs.
Carbide
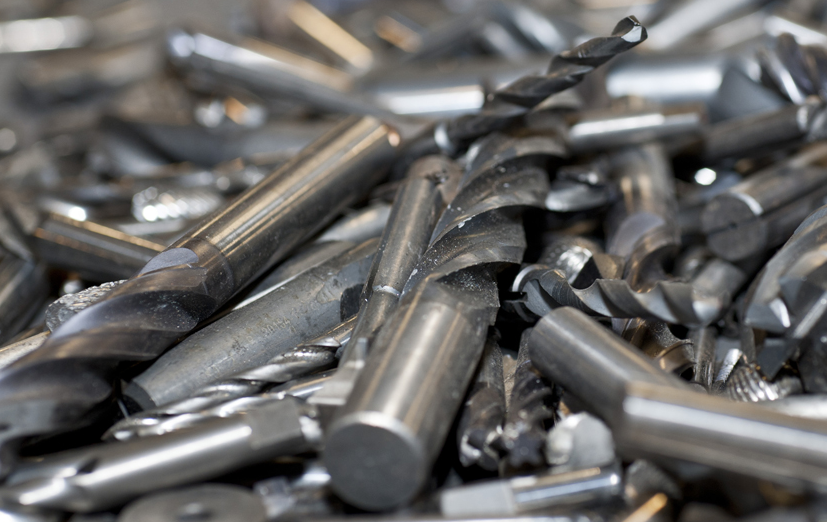
Carbides are compounds produced by combining carbon with other metals that are less electronegative than it or similar to it and have many uses in industry.
For instance, titanium and tungsten are important in the end mill manufacturing industry and are used to coat metals in the milling process.
Should I Choose Carbide-coated End Mills or HSS End Mills?
We assure you that carbide is much more preferred and worthy in CNC milling.
Coated carbide may be more expensive than HSS material. However, they can do milling more rigidly and efficiently. It can achieve 2-3 times more productivity than the HSS one.
The long tool life of carbide end mills will also prove worth your investment in carbide end mills.
Coating of carbide end mills
Adding coats to your end mills leads to higher performance.
Coatings help reduce friction and protect the carbide from the heat generated during cutting. Some coatings are better suited for certain materials.
For example, AlTiN has hardness stability of 4000HV and thermal stability of up to 1200℃. Paying attention to the manufacturer’s recommendations is the easiest way to ensure your coating’s performance.
To Sum Up
We have discussed how to choose the right end mills from the aspects of parameters, shapes, and materials. Finding your right end mill is a complex thing.
Therefore, the factors mentioned above must be kept in mind, and trust only reputable business partners like Tianzhao.
Tianzhao helps factories, traders, and brand owners complete their tool production through high-quality milling cutter manufacturing.
We hope this guide will be helpful for you to find the best end mills on the market.
Please feel free to contact us know if you have any questions.