Due to the large increase in domestic demand for stainless steel products, stainless steel production has also increased significantly. The global growth rate of 5% per year has almost doubled in the past 10 years. With the increase of stainless steel products, the problems of stainless steel processing and manufacturing are becoming more and more prominent, and various manufacturing companies have also invested a lot of time and resources to find better ways to meet this challenge. How to choose a stainless steel milling cutter? What are the characteristics of stainless steel milling cutters?
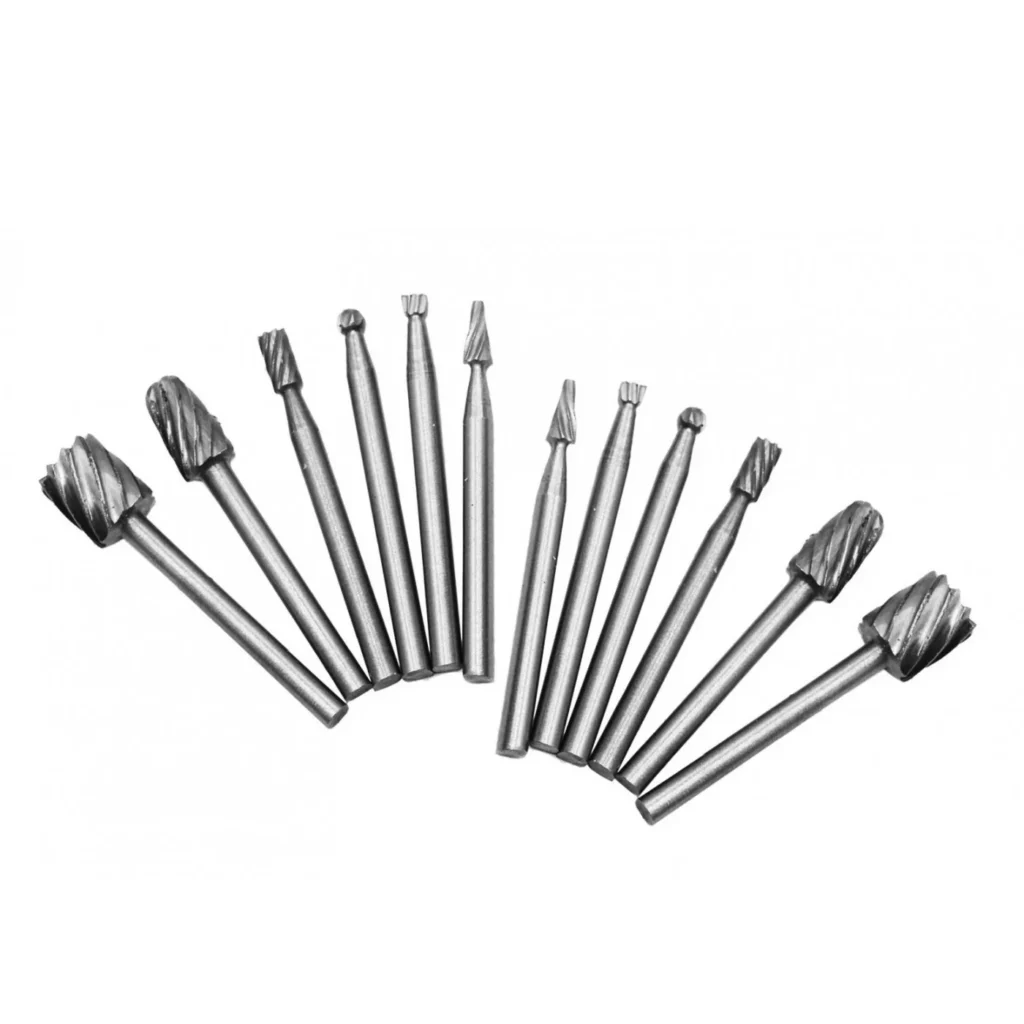
The Main Problems Facing Stainless Steel Processing Are the Following:
Problem
High temperature, high strength, high possibility of processing hardening tendency
The reason
Compared with ordinary steel, stainless steel has low strength and hardness, but because it contains a large amount of Cr, Ni, Mn and other elements, it has high plasticity and toughness, high-temperature strength, and a high possibility of hardening during processing. Cause a lot of loads. In addition, during the cutting process of austenitic stainless steel, some carbides will be precipitated inside, which increases the wear of the cutting tool.
Problem
High cutting force
The reason
The plastic deformation of stainless steel during cutting is large, especially austenitic stainless steel (the elongation rate is more than 1.5 times that of No. 45 steel), which makes the cutting force increase.
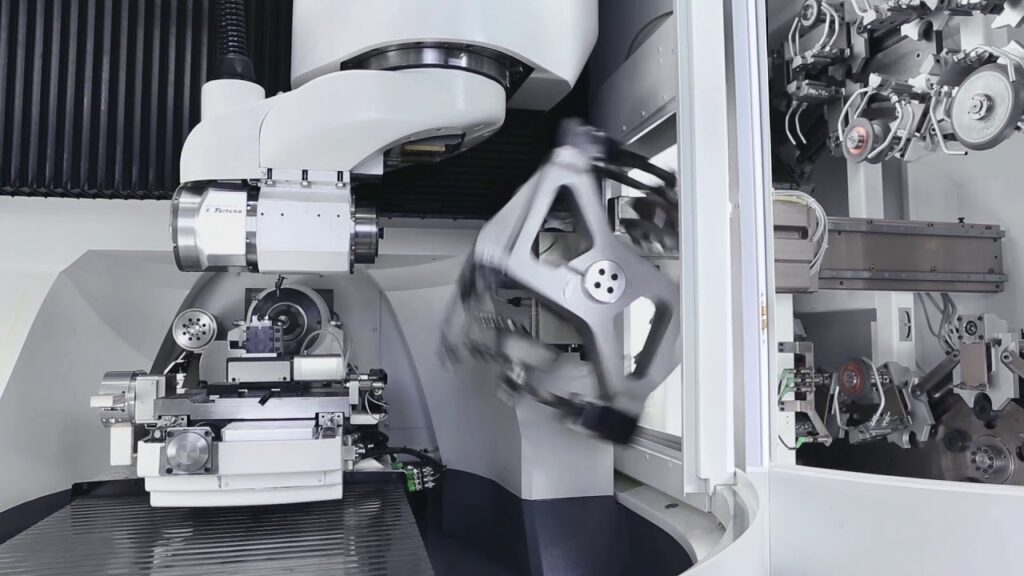
Problem
Serious bonding with cutting tools during the cutting
The reason
It is easy to generate accumulated tumors during cutting, which not only affects the roughness of the processed surface but also easily causes the tool surface to peel off.
Therefore, when processing stainless steel products, we must consider the choice of tools and processing applications, summarized in the following table:
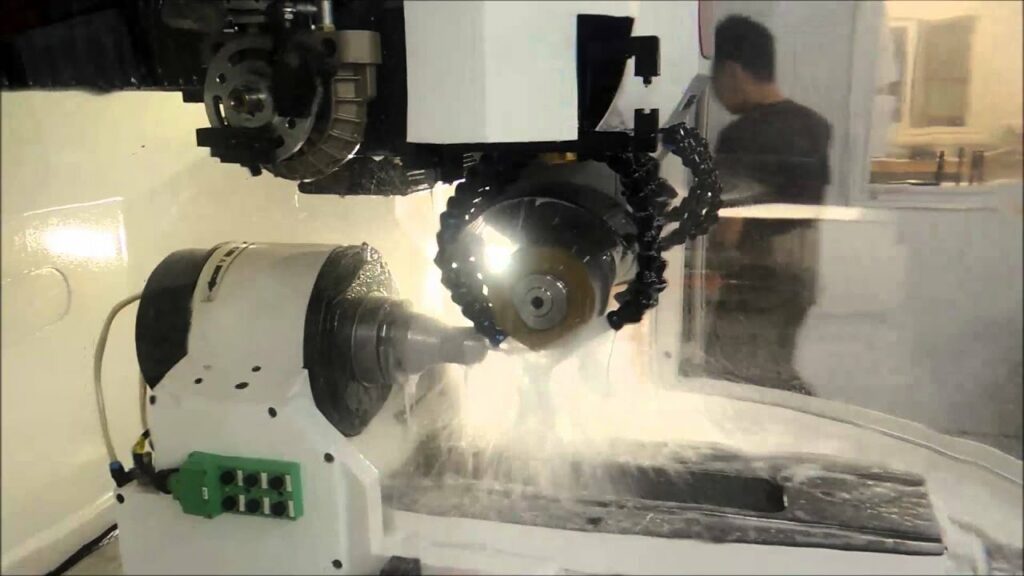
Select Type
Tool material selection
Specific Instructions
1. Choose tool materials with high hardness, toughness, heat resistance, and low chemical affinity with stainless steel.
2. Use hard gold materials, YT alloys are not suitable, and YW or YG tungsten-cobalt alloys containing Ta (Nb) are preferred.
Select Type
Tool geometry parameter selection
Specific Instructions
1. The rake angle and rake angle should be large to reduce cutting deformation and friction with the flank face.
2. The negative chamfer should not be too wide.
3. Adopt a full arc-shaped chip breaker to increase the rake angle to achieve good chip breaking effect.
4. The tool with closed chip holding should increase the chip holding space properly.
5. When sharpening, the roughness value of the surface group with smaller front and back blades should be ensured.
Cutting dosage selection
1. The cutting speed should not be too high. To reduce cutting temperature
2. The feed rate should not be too large to avoid excessive cutting load
3. Eat the knife as big as possible. Invited to open the rough skin or the work hardening layer of the previous process
Appropriate heat treatment of the workpiece
Martensitic stainless steel can be quenched and tempered, austenitic stainless steel can be treated by solution treatment
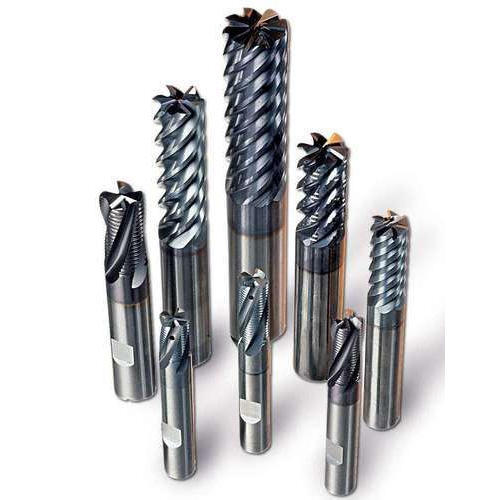
Cutting fluid selection
Use cutting fluid with good anti-adhesion and cooling performance, such as emulsified fluid containing extreme pressure additives such as sulfur and chlorine. The liquid supply must be sufficient. Spray cooling and high-pressure air cooling are preferred. Efficient cooling methods such as cold air cooling.
What Milling Cutter Is Used to Process Stainless Steel?
Carbide materials are used to process stainless steel, and tungsten-cobalt fine-grained or ultra-fine-grained cemented carbide containing TaC or NbC should be used. Such as YG6x, YG813, YW4, YD15, and so on.
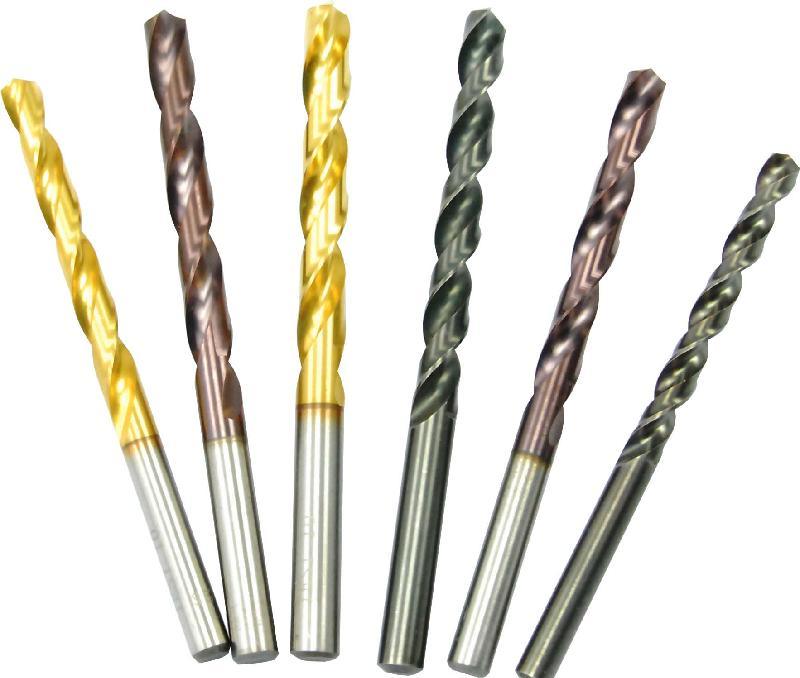
HRC65 Nano Coating Carbide End Mill
When milling stainless steel, extreme pressure emulsion or vulcanized cutting oil should be used. The milling speed of the stainless steel milling cutter made of cemented carbide should be 40~60m/min. In order to avoid cutting the cutting edge in the hardened layer and accelerate tool wear, the feed should be greater than 0.1mm.
Some manufacturers will use high-hardness tools to process stainless steel. In fact, for ordinary stainless steel materials such as 304 and 202, carbide tools can be used. If processing 316 stainless steel, quenched and heat-treated stainless steel, imported and high-hardness stainless steel, in addition to using high-hardness tools, machining stainless steel requires a sharper cutting edge, and try to use special stainless steel knives of well-known brands.
The choice of cutting is very important when machining stainless steel tools. If you want to ensure the performance of stainless steel milling cutters, you must do every step.