Table of Contents
Introduction:
Have you ever wondered how metals are formed into unique and beautiful shapes? Many of us have been stumped about how to drill holes or remove things from hard metals. But before learning the process, it would be best to understand the considerations and selection principles in selecting a milling cutter.
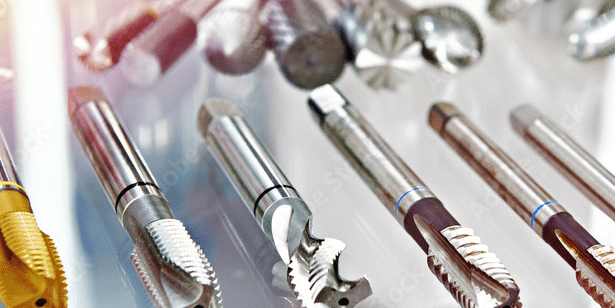
What is milling?
Milling is a mechanical procedure that uses cutting tools rotated at high speeds. Milling is one of the processes of shaping and drilling holes into metal.
There are various types of holes that you can make from milling. Milling can be used on various metals and work pieces. There are some exceptional cases where materials require a special milling tool to be designed. It is essential to know if the object being milled is compatible with the machine and the cutter you plan to use.
Below is a video that can help you understand more about what is Milling:
What is Milling (machining)?, Explain Milling (machining), Define Milling (machining)
What is a milling cutter?
Milling is one of the most challenging jobs, partly due to the fact that millers must have the pre-requisite skills to know which milling cutters to use. But first, what is a milling cutter?
A Milling cutter is the part of a milling machine responsible for cutting and removing the parts that we do not want from a specific part of the material. Milling cutters can have a horizontal or vertical motion. It all depends on what cutter you are using.
Without the milling cutters, milling machines cannot operate due to a lack of blades. Milling tools or cutters are also used to form surfaces required in many industries. There are many kinds of milling cutters with different sizes and shapes that can be used in various jobs.
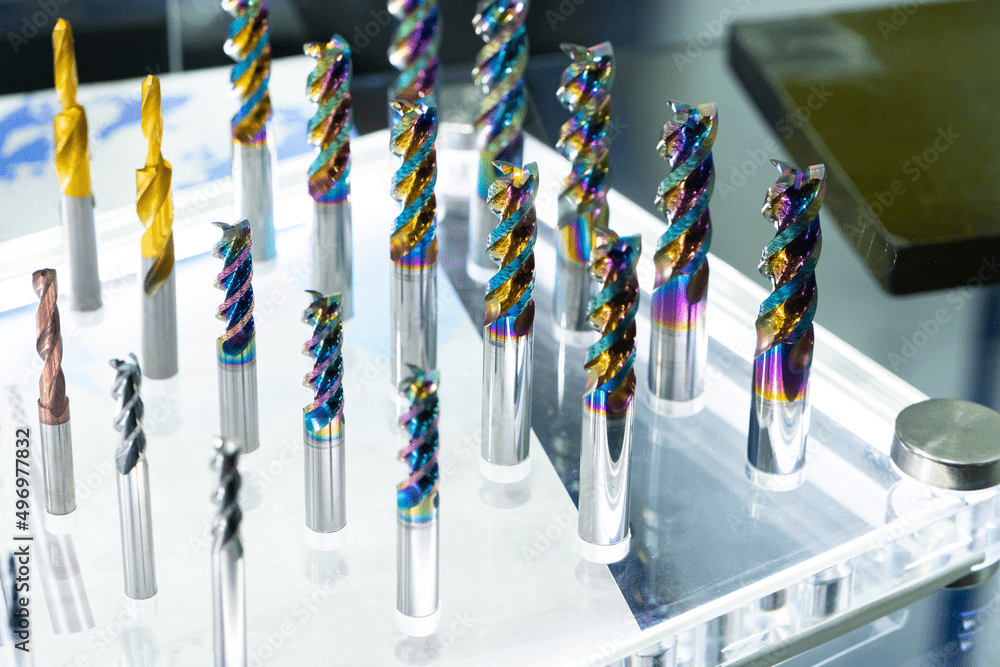
Introducing 6 common types of milling cutters and uses:
1. End milling cutter
An end-milling cutter has teeth at both the end and the sides of the blade. End-mills are used in standing or vertical milling processes. In creating end mills, materials such as high-speed steel or cemented carbide are good choices but not relatively considered the best.
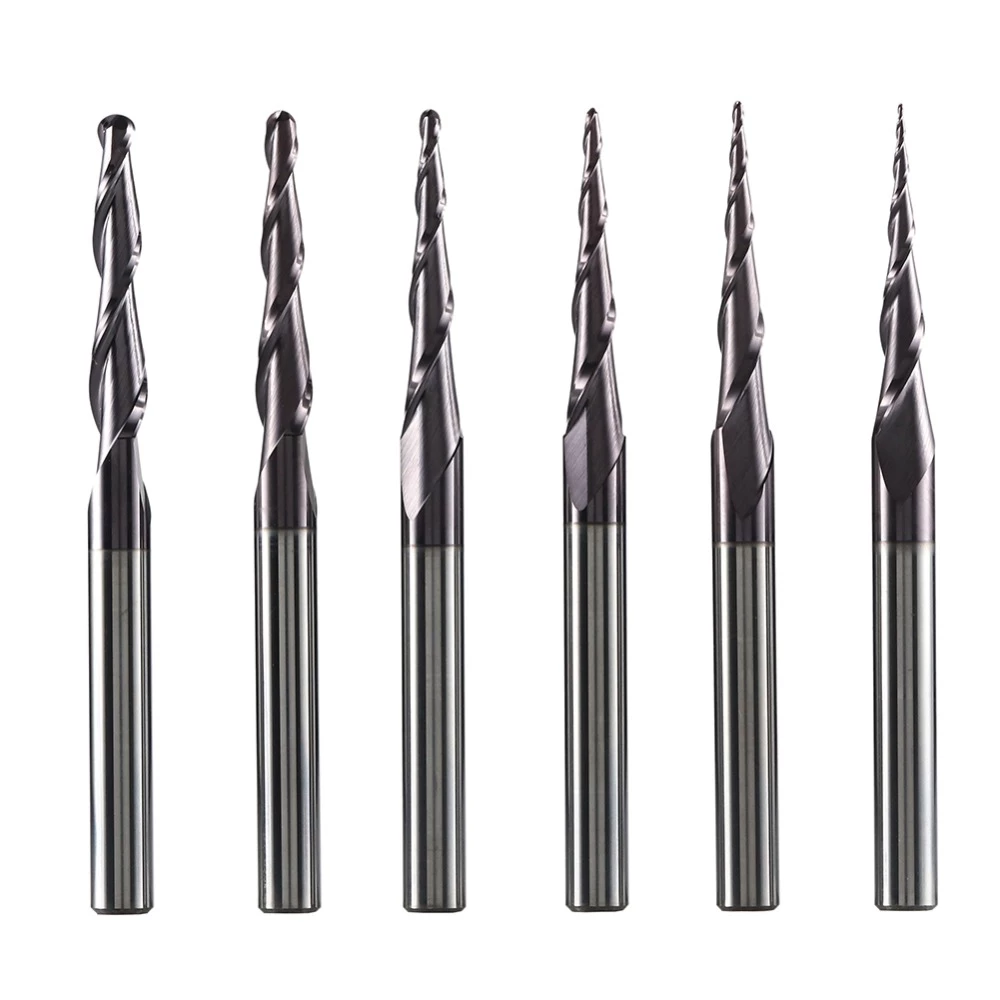
2. Rough-end cutter
Rough-end cutters, also known as ripping cutters, are a type of milling cutter with jagged teeth, which means cutting a workpiece can be done faster. This cutter can eliminate vast amounts of material from a workpiece in a short amount of time.
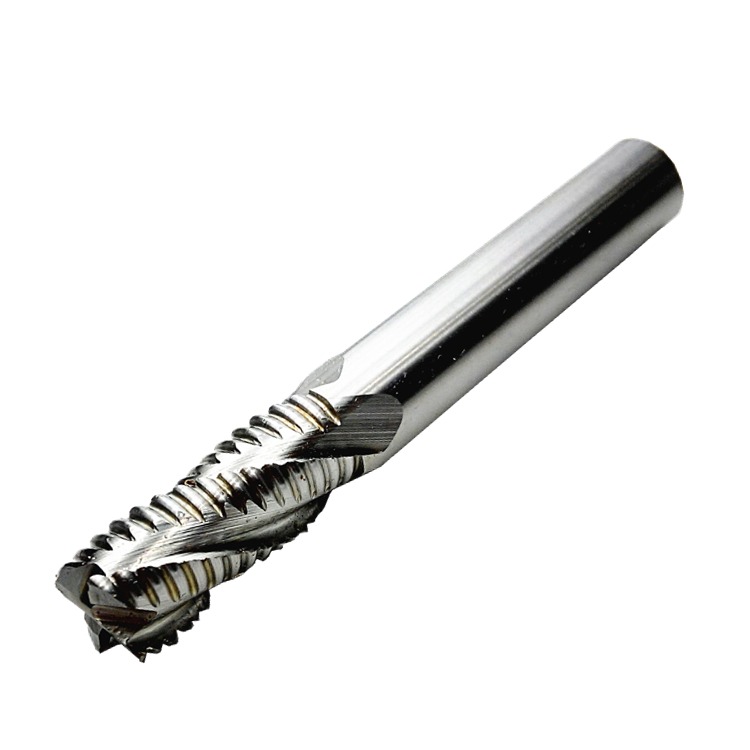
3. Ball-end cutter
Another type of milling cutter is the ball-end cutter, also known as the ball-end mill. They have a hemispherical shape at the end of the blade. This cutter reduces the amount of stress on a workpiece, and it is perfect for three-dimensional milling shapes.
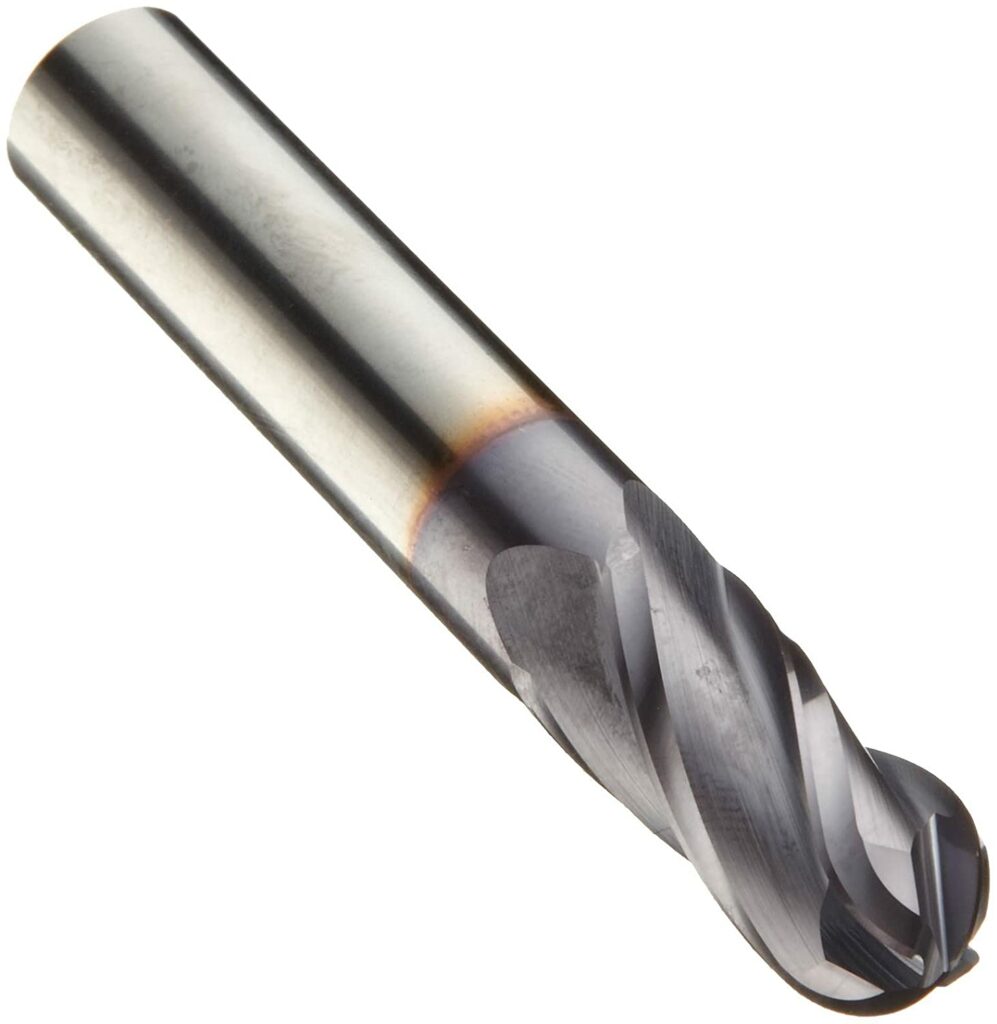
4. Hollow milling cutter
A hollow milling cutter is a pipe-like cutter with thick walls. This kind of milling cutter has its teeth in the inner part of its cylindrical shape. Hollow milling cutters are used for creating screw machines.
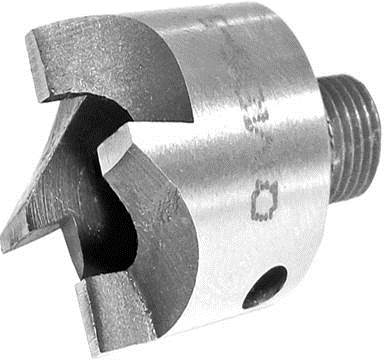
5. Woodruff cutter
A woodruff cutter is a milling tool used to cut keyways for woodruff keys into workpieces made of hard materials, like metal, steel, and aluminum.
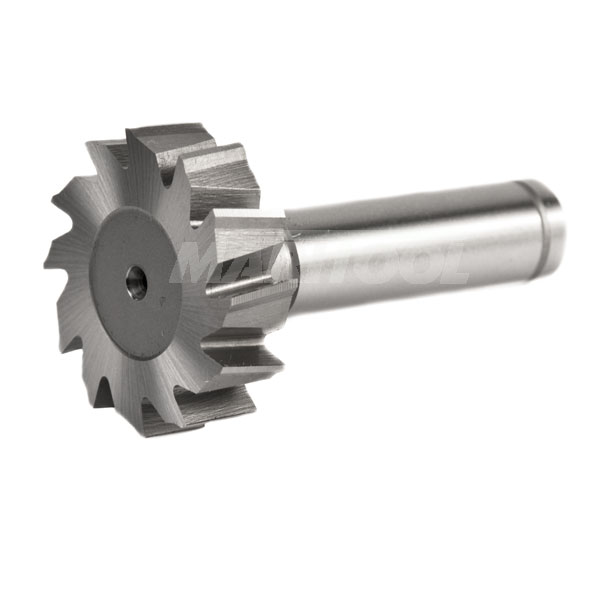
6. Thread mill cutters
Thread mill cutters are one of the many types of milling cutters. They are used for producing and cutting a thread by milling in a helical motion.

Below is a video to have a more in-depth insight into the types of milling cutters Different Types of Milling Cutters & Operations Explained
6 Selection Principles to consider in choosing a milling cutter.
We must know that for something to last a long time, we need to choose the best quality that we can find to maximize the tools we are buying. Here are some of the principles you need to consider when selecting and purchasing a milling cutter for your next business.
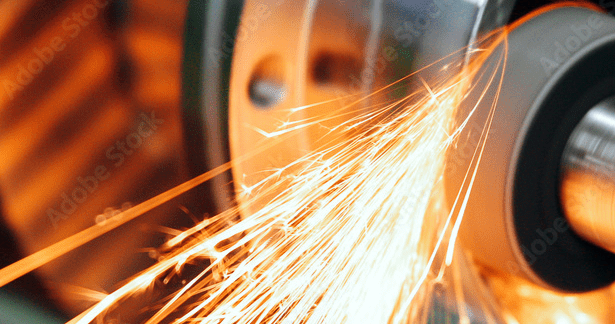
Identifying what milling method or process you need to use:
Identifying the milling method is one of the ways you will choose a milling cutter. You will not know what cutter suits a job if you are wholly unaware of the work you will be doing in the first place.
A milling cutter can be a very expensive waste if the blade you buy does not suit the process of milling. A common mistake that people make is using a tool for a job not suitable for that kind of milling method, which results in the CNC job taking a longer time to finish.
Selecting the size of the milling cutter
The cutting power of milling tools has different variants of strength, and speed, depending on the machine you will use. The most common mistake made when purchasing a milling cutter is getting the wrong size.
If you are new to selecting milling cutters, the machine tool may be too large or too small for the milling cutter to fit, which makes the milling cutter unusable.
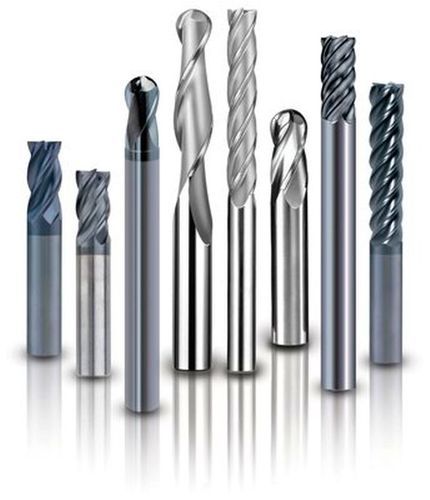
The number of teeth and flutes
The number of teeth and flutes must also be kept in mind. Teeth and flutes are also important in milling cutters. It simply means, that the more teeth it has, the faster it can remove material from a workpiece.
Selecting the materials for the tools
Most milling cutter tools are made of carbon steel, high-speed steel, and solid carbide.
Regular carbon steel is one of the least prioritized materials for a milling cutter. This is a cheaper material for low-phase operations.
On the other hand, high-speed steel is a material that is one of the longest-lasting. This material is more expensive than others, which helps in the long run, by it having a higher rate of removal for workpieces. High-speed steel is a better choice than any other material.
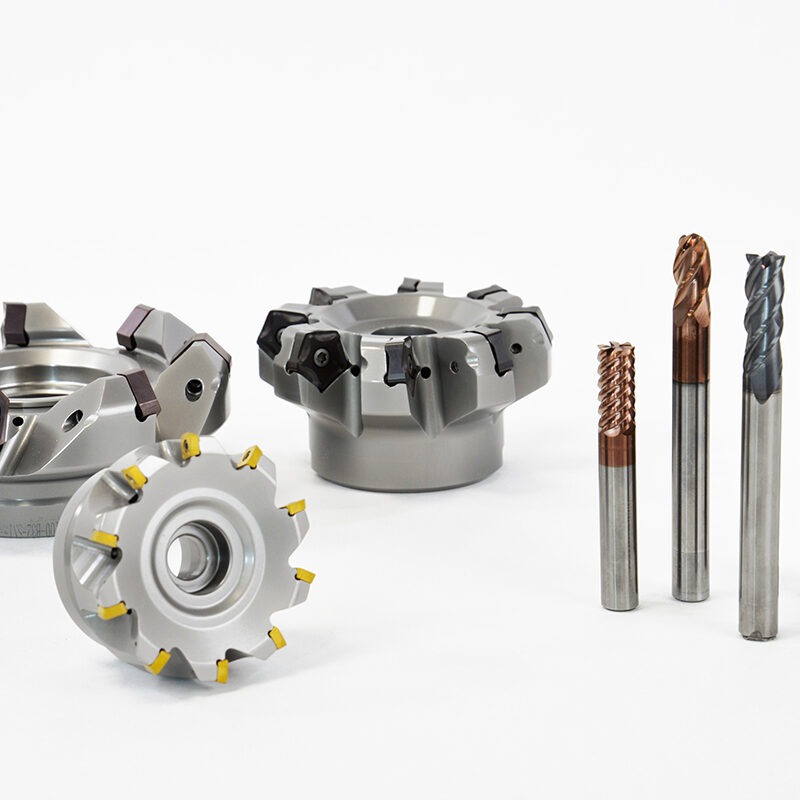
Durability and life of the cutter
If you are looking for a long-term tool and cutter, you must know how to balance the right amount of value with durability. Lower prices don’t always equal the best option as its quality has most likely been sacrificed due to cost-cutting. The durability and the life of your
milling cutter will matter the most as time goes by.
Most cheap milling cutters don’t perform well in the long term and don’t last long. It is more beneficial to look for a tool that can possibly last a lifetime in most cases.
The tools’ coating
Why do we need a coating on cutters in the first place? Every tool that is made needs protection to last a long time. Milling cutters are no exception.
Here are some reasons why we need coatings. The first reason is that it minimizes the stickiness of materials while milling.
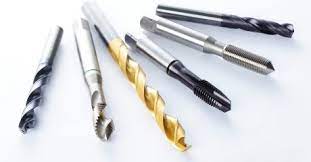
Next, it lessens the friction and protects the tool from the heat while milling. It also hardens the surface of the milling cutter, which makes it last longer. Lastly, it prolongs the life of the tool.
Here is a detailed video explanation of why tool coatings are essential:
Tormach explains tool coatings
Frequently asked questions about milling cutters
These are some often-asked questions concerning milling cutters.
There’s a huge advantage in knowing the answers to these questions.
Being knowledgeable in this area can put your well on your way to selecting your own milling cutters for a project!
What are the most common types of milling cutters?
End milling cutters, ball end milling cutters, and rough end milling cutters are the three most common types of milling cutters.
Why do you need a milling cutter?
Milling cutters have a variety of jobs, sizes, and specialties; milling cutters are used for removing hard materials from a workpiece so that they can be shaped and perfectly formed into a new form that can be used in a variety of ways.
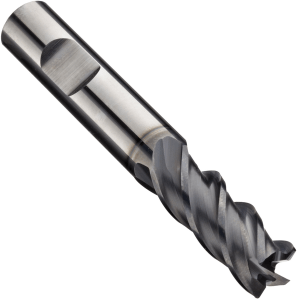
How does Milling work?
Milling is a process or work involving milling machines, milling processes, and milling cutters. Different approaches and devices are used to cut a particular workpiece with a specific type of material into a complex workpiece. Typically, these workpieces are metals: steel, aluminum, etc.
How do you prolong a milling cutter?
A milling cutter is one of the tools that need care. You can prolong the life of your milling cutter by knowing the following:
- Run your tools at a constant speed. This is prescribed on the manufacturer’s label.
- Coat your tools. This practice helps protect your tools from heat and hardens the cutter surfaces.
- Coolants are very important. These liquids cool the tools you are using to protect them from high temperatures during the milling process.
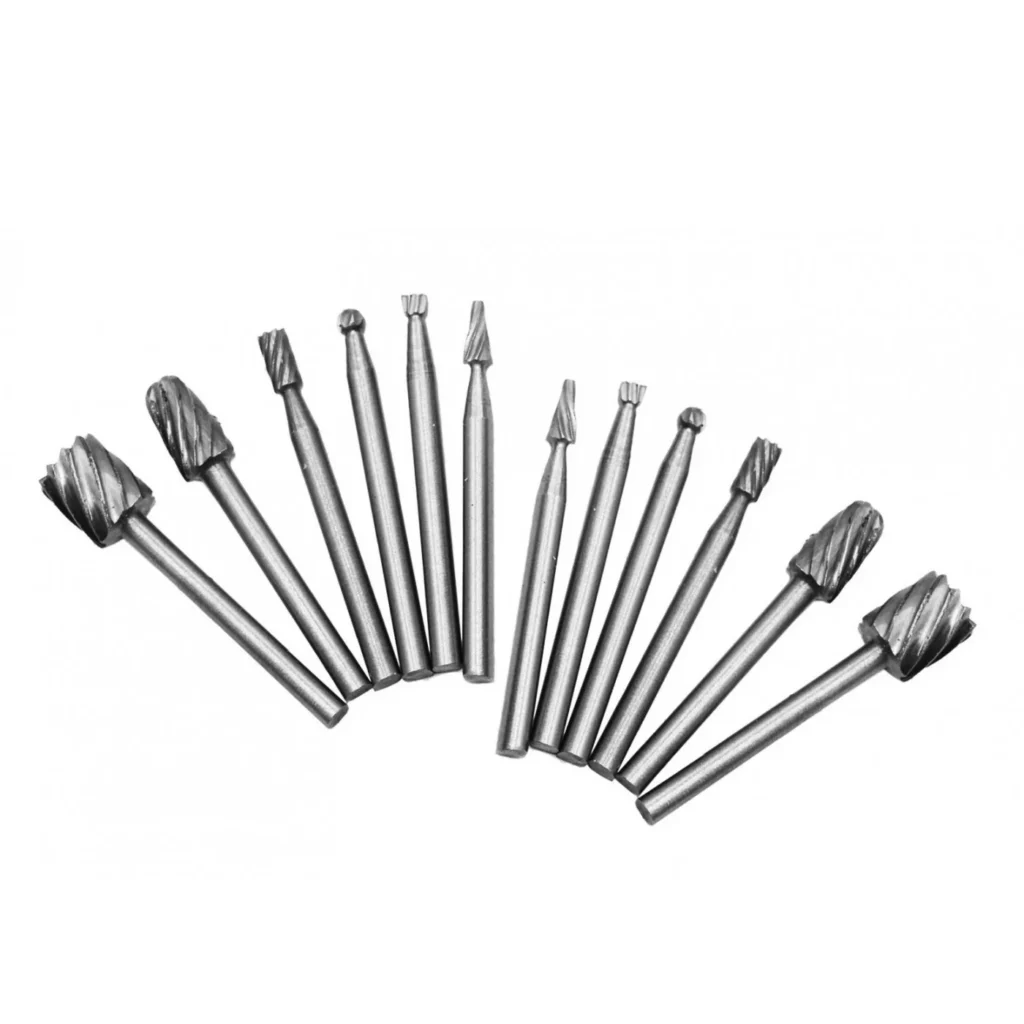
Summary
Milling cutters are pretty expensive, so we need to know how to prolong their lives and durability. Thus, everyone must be aware of how to correctly choose one by keeping in mind the considerations and principles related to selecting a milling cutter.