When you’re picking out cutting tools, the first challenge is to figure out which style to buy. The second is to select what material and coating combination you’ll need. You might be questioning why coatings matter – surely it’s just a marketing ploy to get you to spend an extra couple bucks, right?
Wrong.
Much like a Rain-X coating on your windshield will help water bead up and fly away, different coatings use their hardness to make chips fly faster and tools dull slower. There are many different coatings, which we will get to in a minute, but there are two basic categories describing how the coating is applied to the tool – physical coatings and chemical coatings.
Physical coatings: Also referred to as physical vapor deposition (PVD) coatings, physical coatings are great for cutting tools that don’t get really hot, such as high-speed steel tools. These coatings are typically thinner and include Titanium Nitride, Titanium CarboNitride, Aluminum Titanium Nitride, and Chromium Nitride coatings.
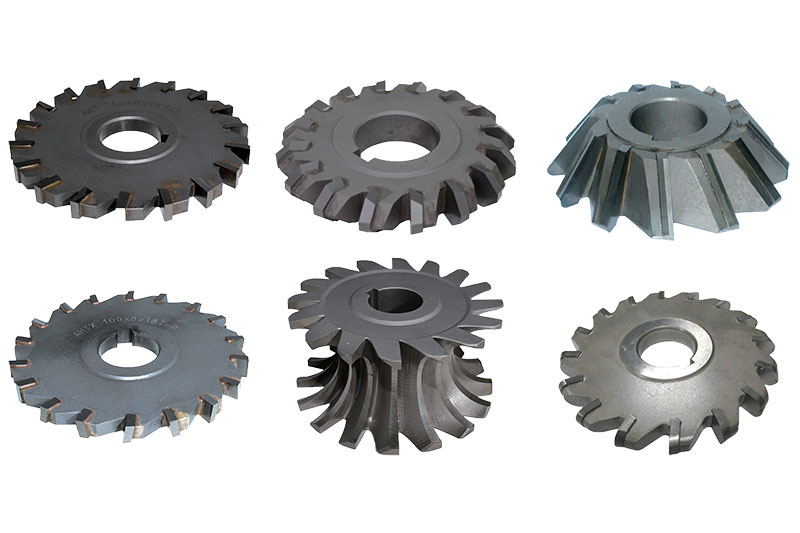
Chemical coatings: Chemical coatings, also called chemical vapor deposition or CVD coatings, are ideal for cutting tools that get hot. Lathe tooling is a good example. These coatings are applied with plasma or photo-induced processes at extremely hot temperatures (about 18000° F). The result is a precisely uniform coating that strongly adheres to the cutting tool’s surface.
MILL CUTTING TOOL COATINGS
The more visual part of the selection process is the color of the coatings.
TiN coating titanium Nitride: Titanium Nitride (TiN) coatings are gold in color. They are the most commonly used coating because the ceramic base is hard and heat resistant. You’ll use these for general-purpose drilling.
TICN Coating
Titanium CarboNitride: Titanium CarboNitride (TiCN) coatings are harder than TiN and create less friction with most materials, so you’ll want to use these when you cut aluminum and other gummy metals.
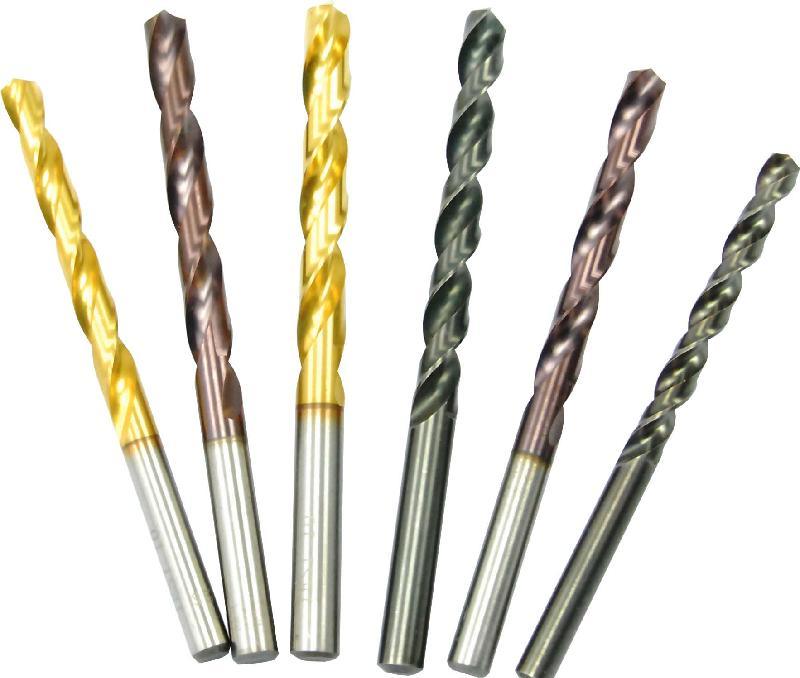
CrN coating
Chromium Nitride: Chromium Nitride (CrN) coatings are silvery and metallic. These coatings offer similar benefits of TiCN, such as creating less friction, but the coating can get hotter than TiCN and still maintain its innate qualities and better lubrication qualities. The best application for this coating is cutting Aluminum since there’s a lesser chance of surface welding.
Aluminum Titanium Nitride:
TiAlN coating
Aluminum Titanium Nitride (AlTIN or TiAlN) coatings are normally dark gray in color. They’re normally used when the job is too hot for Titanium Nitride coated tools because it’s harder and can maintain this hardness at higher temperatures than Titanium Nitride coated tools. This is perfect for cutting steel. You might have heard these tools are more likely to break due to thermal shock, but all carbide end mills are susceptible to that. You’re essentially putting cool coolant on a hot tool, and it can shatter. Some coatings, like Aluminum Titanium Nitride, are more susceptible to that.
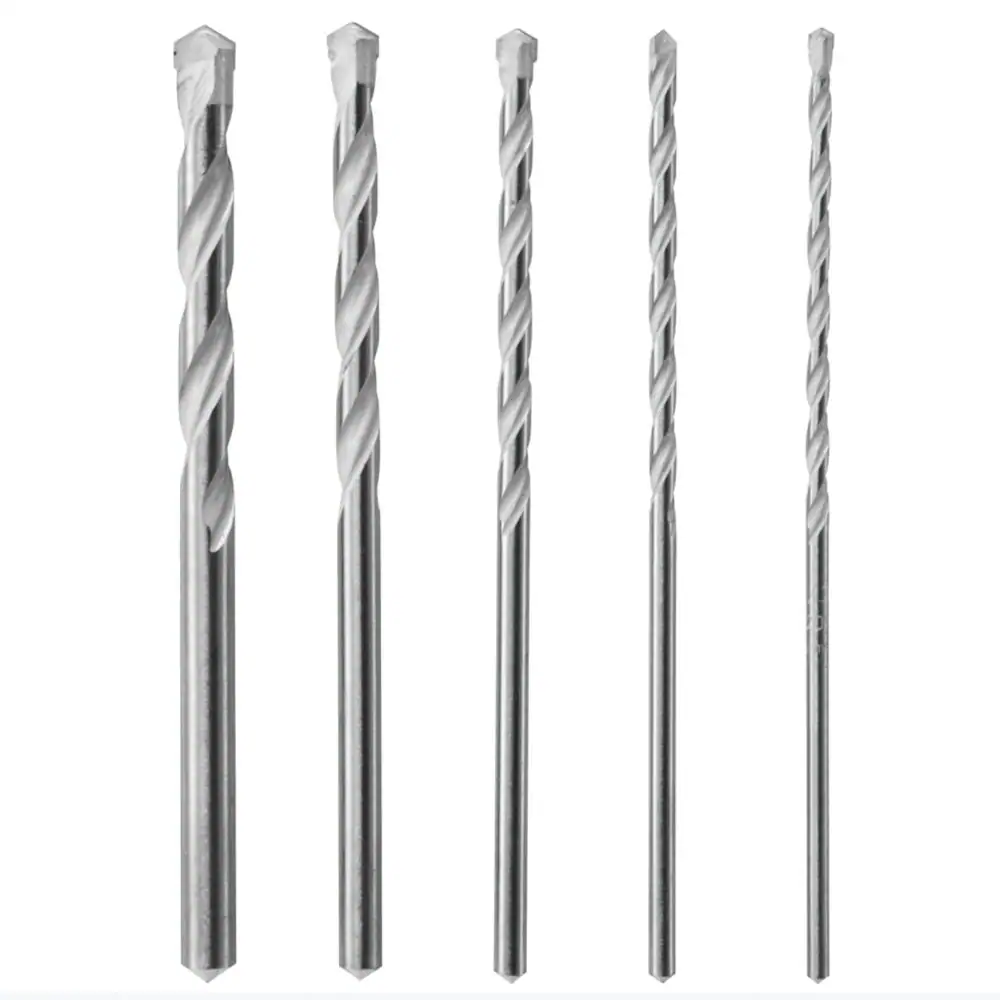
TiAlN Coating
Titanium Aluminum CarboNitride: You’ll be able to identify Titanium Aluminum CarboNitride (TiAlCN) by its pink coating. This coating is a nano-coating, which means it’s extremely hard, and can be used at high temperatures and still yield low friction. That’s why it’s great for stainless steel, cast iron, aluminum, and superalloys.
Oxide
Oxide: Oxide coatings are applied to tools that need help retaining lubrication on the surface to keep the tool cool, such as a tap when using a tapping fluid. You’ll want to use this coating, which looks like a smokey black, for general-purpose tapping applications.
D1119201
Bright or Gloss: If you see a tool assigned with a bright or gloss coasting, it’s just another way of saying the tool is uncoated but that the tools were polished to create a mirror-like finish. This may seem strange since there are so many benefits to coatings, but the asset is you can make uncoated tools very sharp. If you try to sharpen a coated tool, you’ll end up stripping away the coating to get to the tool. This is a great feature if you’re looking to do cutting on a budget.
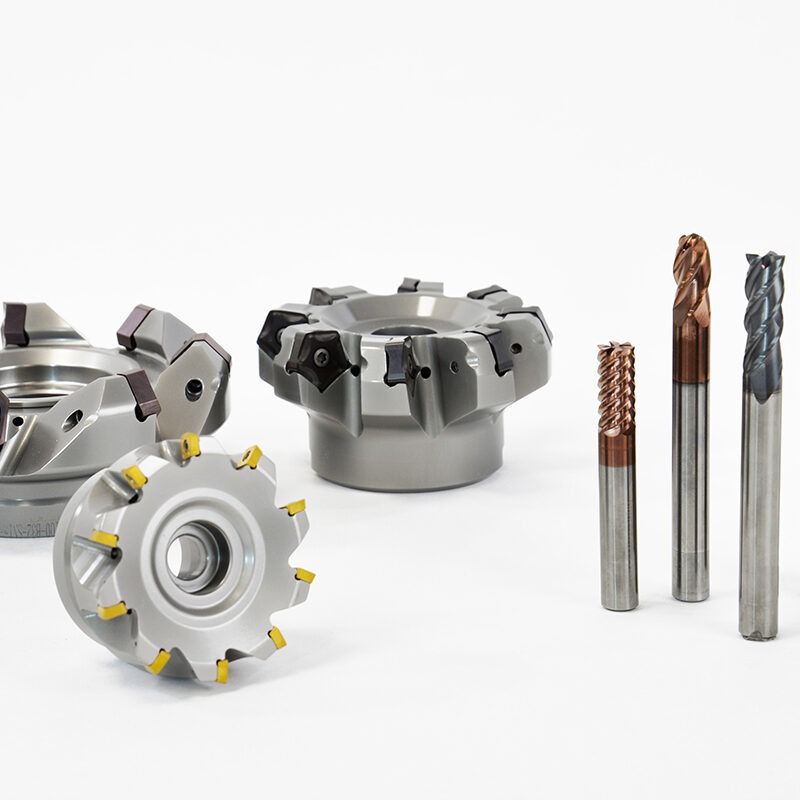
LATHE CUTTING TOOL COATINGS
Lathe cutting tools are coated in a lot of the same coatings as mill cutting tools, such as Titanium CarboNitride and TiCN, but a newer industry development has been offering single and dual coated inserts.
Single Coatings: Carbide inserts are the most common lathe inserts available, and CVD and PVD coatings are applied to make the event more wear-resistant, much like why coatings were applied to mill cutting tools and drills. Coated carbide inserts most often feature Titanium CarboNitride, Oxide, and other coatings used for mill cutting tools.
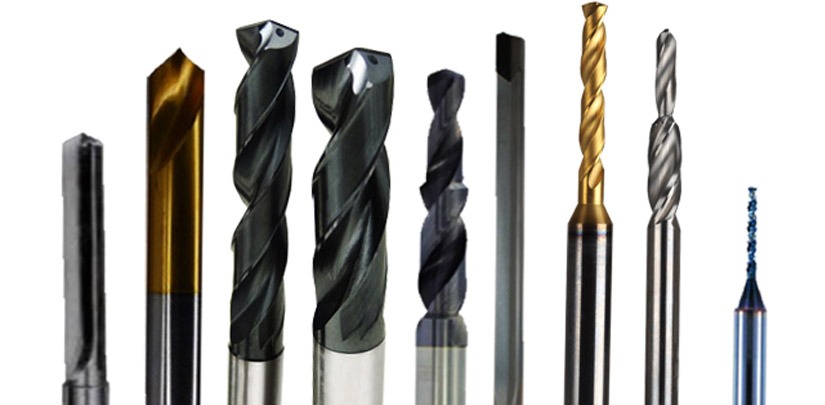
Dual Coatings: The concept behind applying multiple coatings to the same insert is to piggyback off the benefits of multiple materials. For instance, a carbide insert could be coated with Chromium Nitride to increase wear resistance, and then coated with Titanium CarboNitride to reduce friction. Whether or not this is cost-effective has yet to be determined.
This is only the start of a metallurgy-based conversation, and if you have questions, our website has a slew of information to help you with these decisions.