In order to process economical and efficient milling cutters, the most appropriate cutter should be selected and used according to the shape, processing performance, and processing accuracy of the cut material. Therefore, it is necessary to consider important factors such as diameter, number of blades, blade length, helix angle, and material.
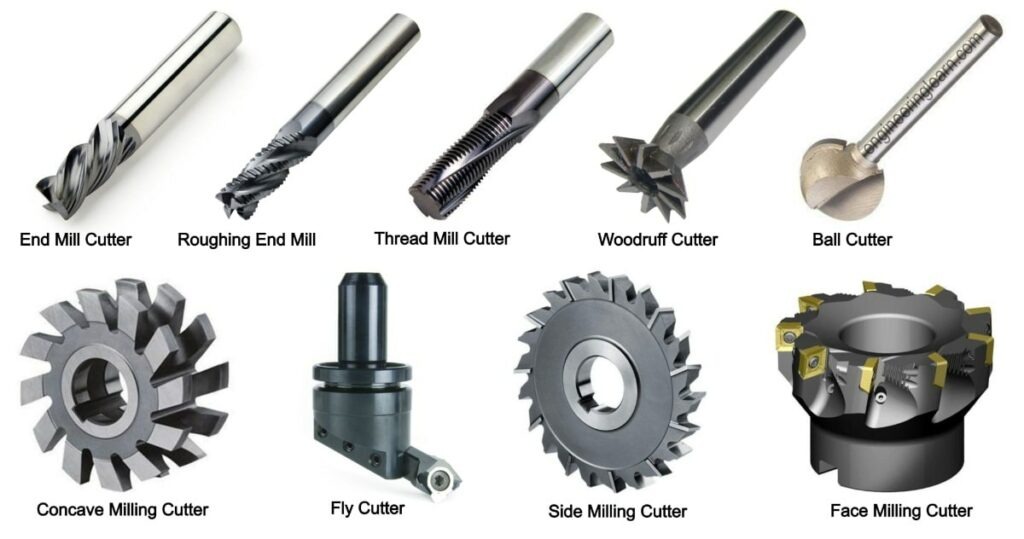
In cutting processing, in order to maximize the processing quality and repeat accuracy, the right tool must be selected and determined correctly. For some challenging and difficult processing, the choice of tool is particularly important.
When machining curved parts, in order to ensure that the cutting edge of the tool and the machining contour are tangent at the cutting point, and to avoid interference between the cutting edge and the contour of the workpiece, a ball-end knife is generally used, a two-edge carbide end mill for rough machining, semi-finishing and finishing For four-edge milling cutters, the number of blades is also related to the diameter of the end mill bits.
A number of edges: An important factor affecting the performance of carbide end mills.
The 2-edge-accommodating groove is large, so the iron cutting discharge is good, but the tool contact area is narrow, so the strength is reduced, and it is mostly used for groove cutting.
The 4-blade-accommodating groove is small, so the iron cutting discharge ability is low, but the tool contact area is large, so the strength is increased, and it is mostly used for side cutting.
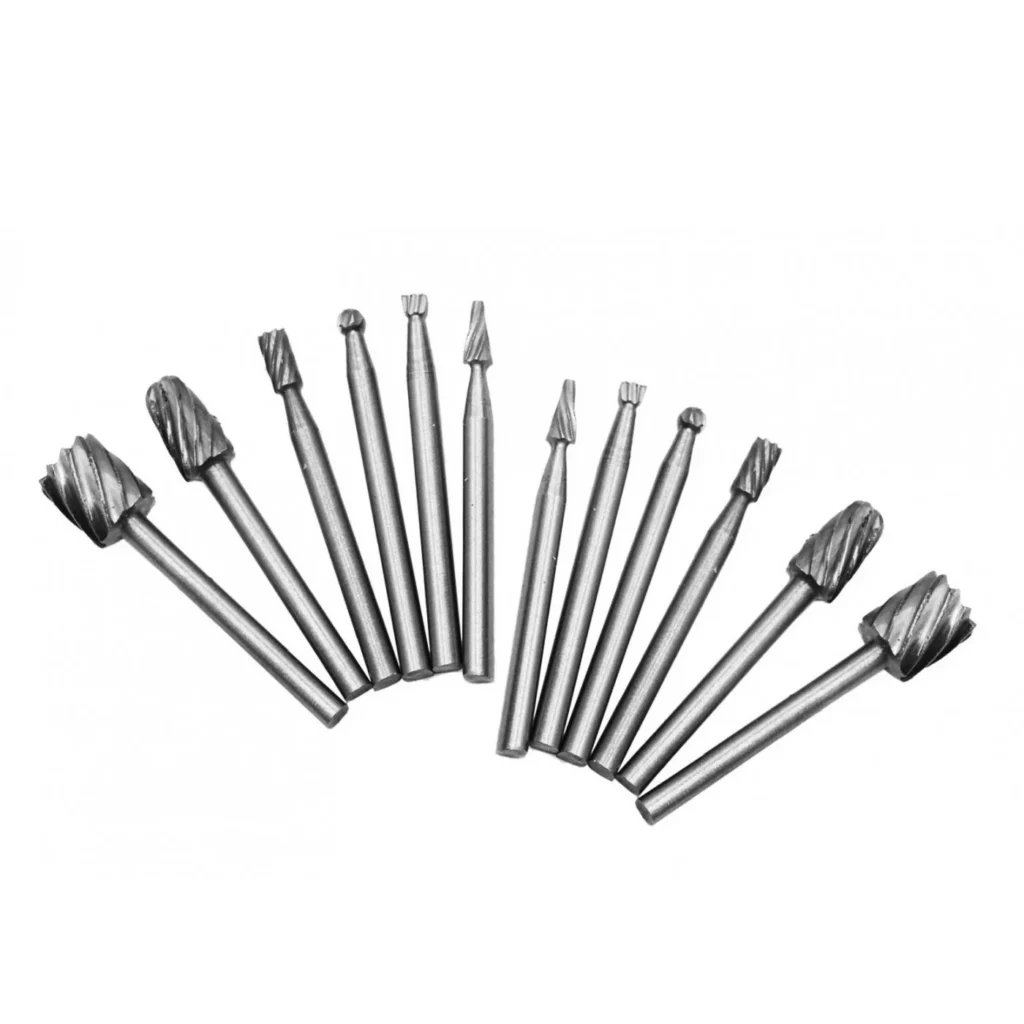
Blade length: reducing the length of the blade during processing can extend the service life of the tool. The protruding length of the milling cutter will directly affect the strength of the milling cutter, so be careful not to machine too long.
Helix angle:
Small helix angle (15°): suitable for keyway milling cutters.
Medium helix angle (30°): widely used.
Large helix angle (50°): high helix angle milling cutter for special purposes.
During processing, too much contact between the tool and the surface of the workpiece is likely to cause the tool to fail quickly. An effective rule of thumb is to use a milling cutter with a diameter of about 1/2 of the narrowest part of the workpiece.
When the radius of the milling cutter is smaller than the size of the narrowest part of the workpiece, the cutter has room to move left and right and can obtain the smallest cutting angle. Milling cutters can use more cutting edges and higher feed rates. In addition, when a milling cutter with a diameter of 1/2 of the size of the narrowest part of the workpiece is used, it can maintain a small cutting angle, and it will not increase when the tool is turned.
The best tool for particular machining depends not only on the material being cut but also on the type of cutting and milling method used. By optimizing tools, cutting speeds, feed rates, and machining programming skills, parts can be produced faster and better at lower machining costs.
Above are the basic knowledge about how to choose the best tool for CNC machining, hope it will be helpful to you. For more information, you can contact Melody!