Even in the precise world of CNC machining, mistakes happen. No one wants to be the person responsible for crashing their CNC machine or spend time recutting a part they thought they had right the first time. As you progress in your career as a machinist, errors become less likely, but the best way to avoid mistakes altogether is to learn from someone else’s.
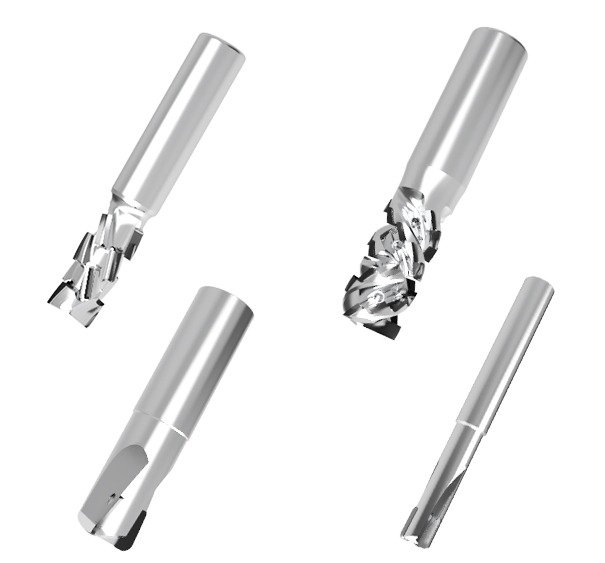
Here, we’ll help you do exactly that by going over eight common headaches machinists working with end mills encounter, how to avoid them, and how to fix them if they do end up happening.
8 Common Machining Headaches (And How to Fix Them)
The following have caused many machinists undue frustration. Follow these tips to make your CNC tooling a little easier.
End Mill Breakage
There are several common causes of end mill breakage. Your feed could be too heavy. Check it and reduce the feed rate if it’s obvious the machine is biting off more than it can chew. The cut programmed into the machine could also be too aggressive; try decreasing the width and depth of your cut to fix this issue.
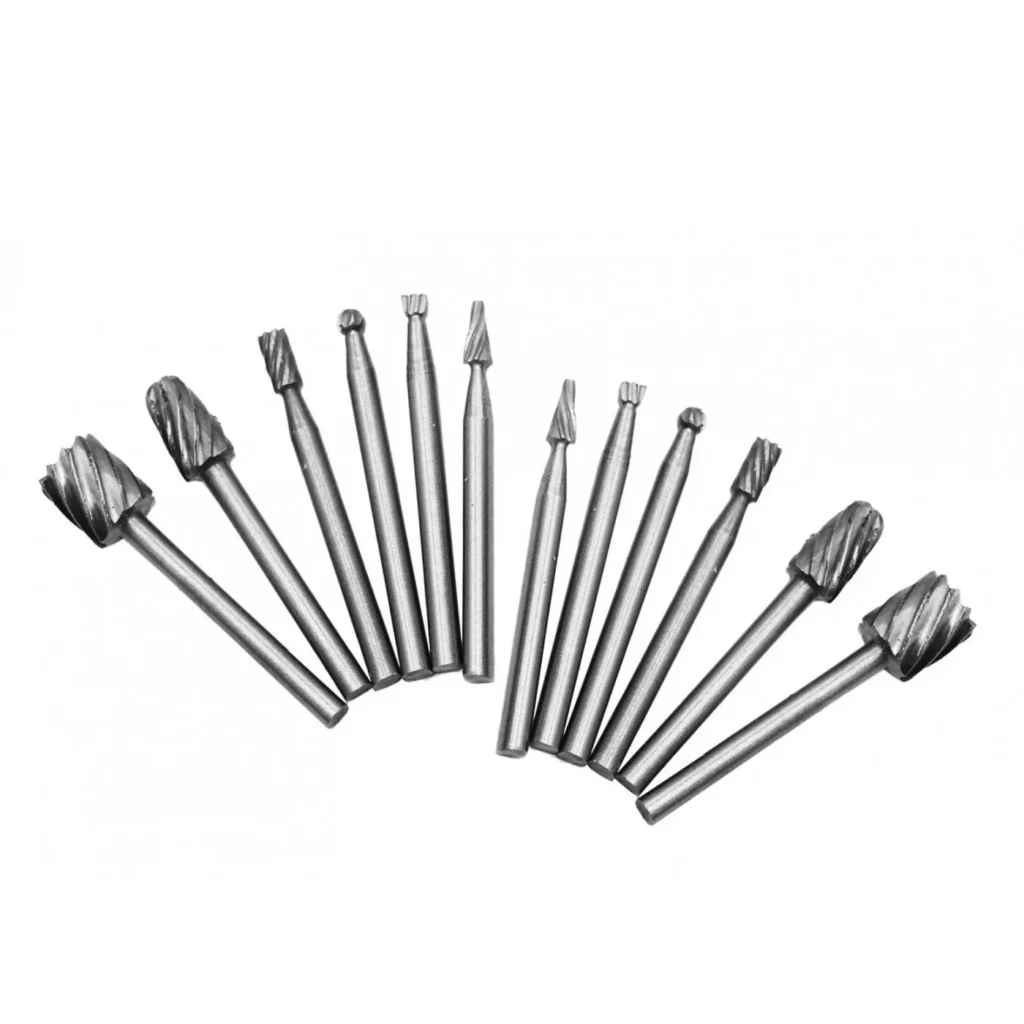
There could also be too much tool overhang, meaning you’d need to hold the shank deeper or use a shorter end mill for your work. And lastly, the cause could be simple wear and tear. If your carbide cutting tool is too dull, it’ll break. Make sure you check it consistently and sharpen it before it becomes too worn down.
Unusual End Mill Wear
Check the following simple things to see which one of them can cause unusual wear on end mills:
Speed and rates could be too high. If so, adjust them accordingly.
If the material you’re cutting is too hard, make sure you’re using a coating like TiAlN or AlCrN.
An incorrect helix angle can cause unusual wear, so check to make sure it’s right if you notice this.
The primary relief angle could be too large. Decrease it to correct the problem.
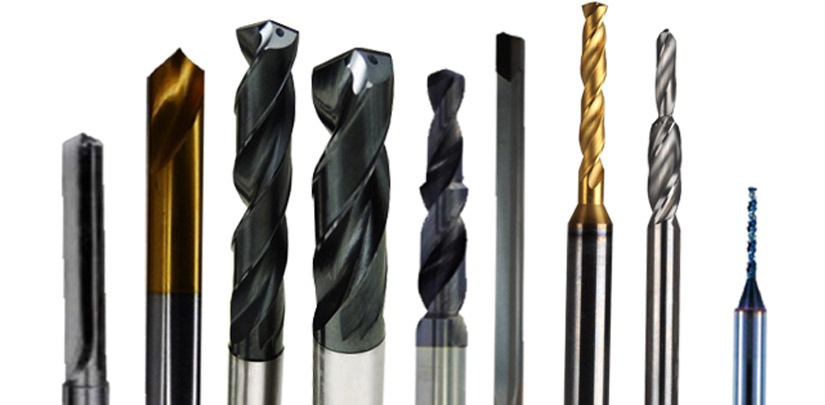
When re-cutting, chips of material can get in the way and cause wear. If you notice that happening, try adjusting the speed, feed, and chip size. You can also clear chips with more coolant and air pressure.
Short Tool Life
If your metalworking equipment is wearing out faster than it should, one of the following could be the culprit:
The cutting friction is set too high.
Cutting hard material without coating.
Incorrectly set helix and relief angles.
Make sure your tools are sharpened, you’re using the proper coating on hard materials, and that your angles are correct.
End Mill Chipping
Heavy feed rate and lack of rigidity can both cause chipping. Make sure you reduce the feed rate if you suspect a problem. You can also try using a shorter tool, holding the shank deeper, or climbing milling.
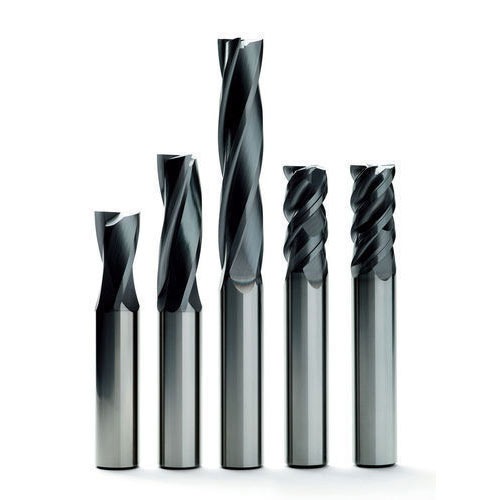
Headache #5: Excess Chip Packing
Check for the following problems if you experience excess chip packing:
The cut is too heavy.
Not enough chip clearance.
Insufficient coolant.
You can try and correct this problem by decreasing the width and depth of your cut, using an end mill with fewer flutes (for chip clearance), or using higher coolant pressure and directing the coolant nozzle at the point of cut. Air pressure can also be used.
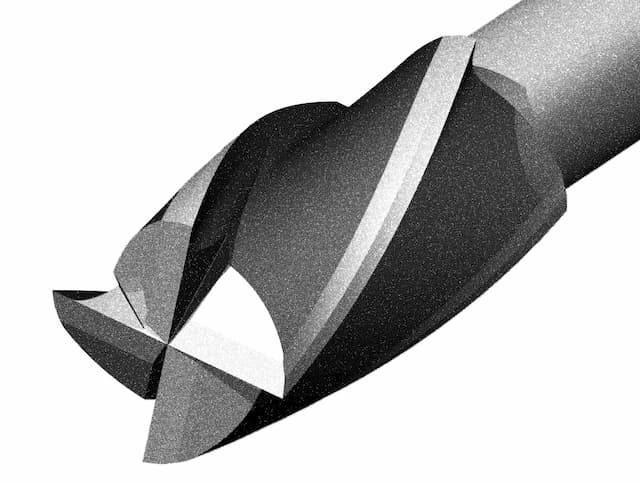
Burrs
If you’re getting burrs, check to make sure your tool is sharpened, that your feed and speed rates are correct, and that your helix angle is set properly.
Headache #7: Rough Surface Finish
Be on the lookout for any of these factors that can cause a rough surface finish:
The feed rate is too heavy.
Slow cutting speed.
Worn tools.
Shallow dish angle on the end of your tool.
If your product has a rough finish, try correcting the feed rate and speed, swapping out a dull tool for a sharp one, or increasing the dish angle on your tool.
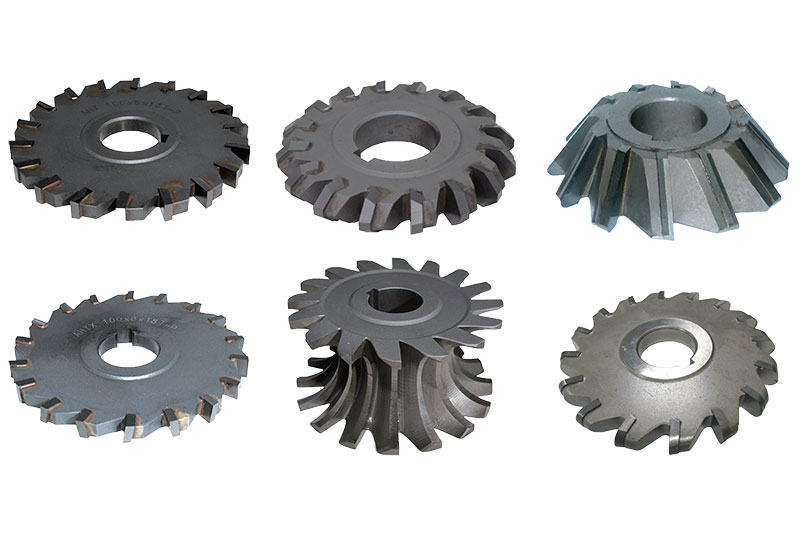
Headache #8: Chattering
Chatter can be caused by:
Feed and speed are too fast.
Lack of rigidity in your setup.
Poor setup in general.
The cut is too heavy.
Too much tool overhang.
Correct for this by making sure your feed and speed settings are correct, improving clamp rigidity, or decreasing the width and depth of your cut. You can also try using a shorter tool, climbing milling, or holding the shank deeper.
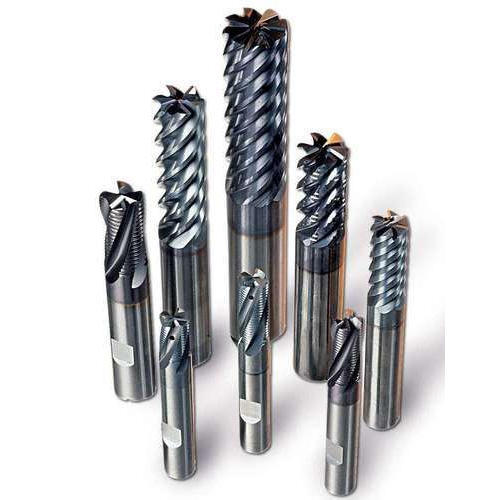
Recap
By checking simple factors like the width and depth of your cut, the sharpness of your tools, and the speed and feed settings, you can avoid a lot of headaches down the line. Staying focused and attentive is the best way to avoid slip-ups on the job.
Recommended Reading
Choosing the Right End Mill Coating for Each Application
When it comes to finding an end mill coating, there are many variables that enter the equation. Understanding this is crucial to finding the right coating.
The Benefits of Resharpening End Mills
Extend end mill life and increase your profit margin all at one time by resharpening your tools instead of replacing them with new ones every time.
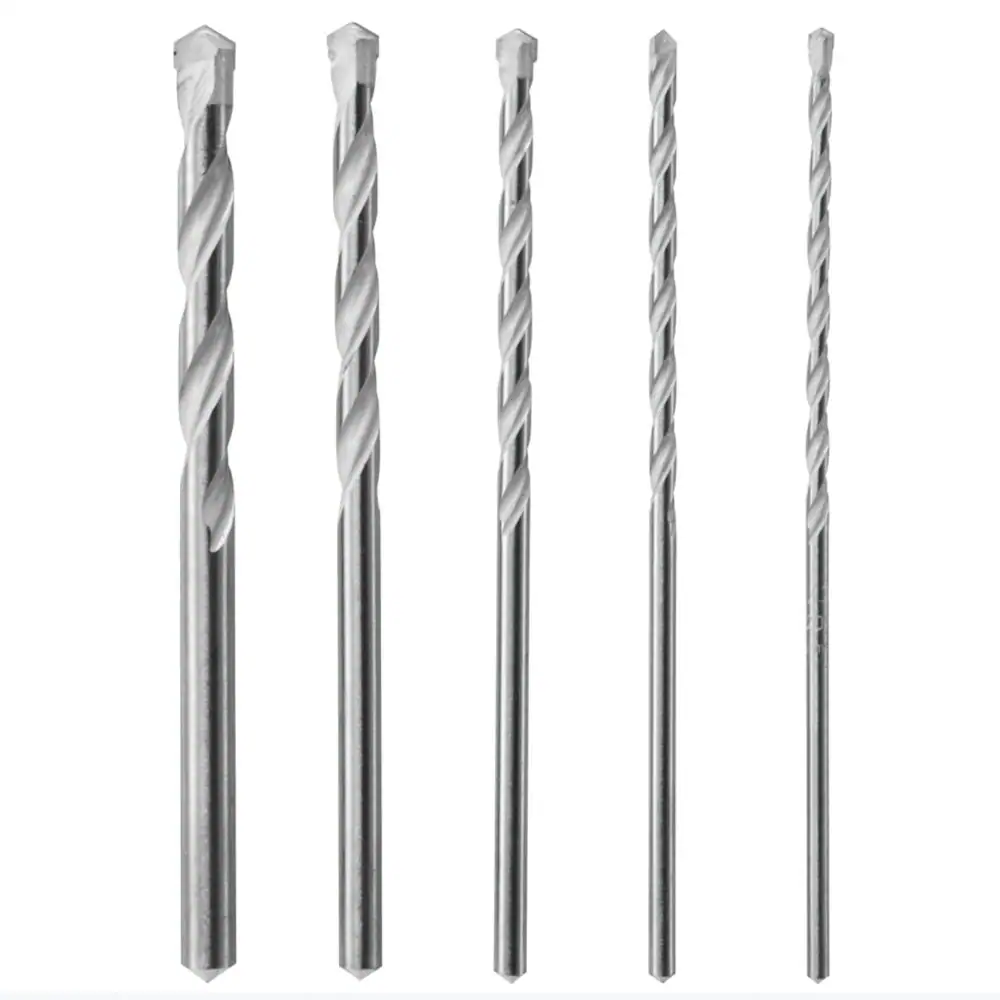
Making the Right Choice When it Comes to End Mill Flute Count
Which endmill flute count is right for your machining job? 2 flutes? 7 flutes? Read this post to know how to choose the correct end mill for the job.
The Difference Between High-Speed Steel & Carbide End Mills
When choosing an end mill for machining the choice often starts with high-speed steel vs carbide end mills. Use this article to pick which is best for you.